Токарная обработка представляет собой технологический процесс обработки деталей типа тел вращения. Вращение заготовки является главным движением, посредством которого совершается процесс резания совместно с поступательным перемещением инструмента (движение подачи). В последнее время находят все более широкое распространение токарные обрабатывающие центры, которые позволяют наряду с классическими токарными операциями выполнять фрезерные и сверлильные операции, а также проводить полную обработку детали за одну установку (это достигается за счет использования приводного инструмента и контршпинделя).
Основные требования к станку:
- Стабильность, мощность и крутящий момент, особенно для обработки больших диаметров
- Закрепление заготовки
- Расположение инструмента
- Время смены инструмента/количество инструментов в револьверной головке
- Ограничения частоты вращения шпинделя (об/мин)
- Наличие контршпинделя или заднего центра
- Возможность использовать люнеты
- Давление подачи СОЖ
Выбор оптимального режима резания
Под оптимальным режимом резания принято понимать такой режим, который обеспечивает наибольшую производительность (наименьшее машинное время). Выбор режимов резания производится в определенной последовательности:
1. Анализ чертежа обрабатываемой детали
- Анализ требований к размерам и качеству обработанной поверхности
- Допуски
2. Анализ геометрии заготовки
- Тип операции (продольная, торцевая и профильная обработка)
- Наружная, внутренняя обработка
- Черновая, получистовая или чистовая обработка
- Стратегия обработки
- Число проходов
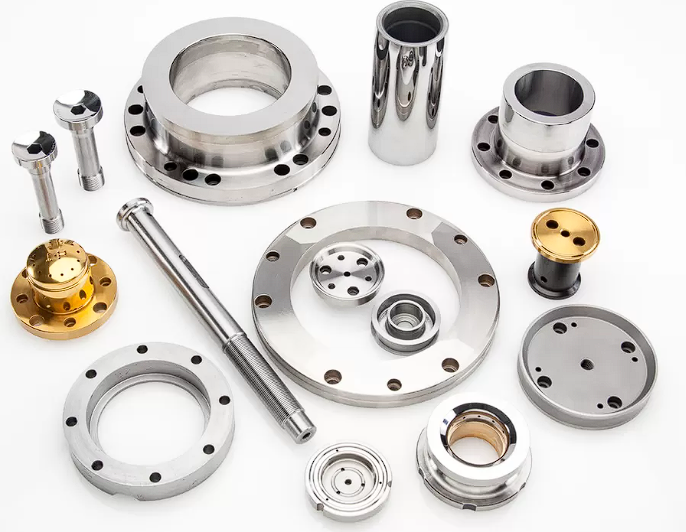
3. Анализ материала заготовки
- Обрабатываемость
- Состояние заготовки (отливка или предварительно обработанная)
- Твёрдость
- Содержание легирующих элементов
- Тип материала
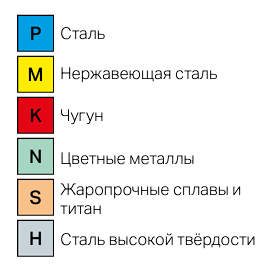
4. Выбор геометрии инструмента
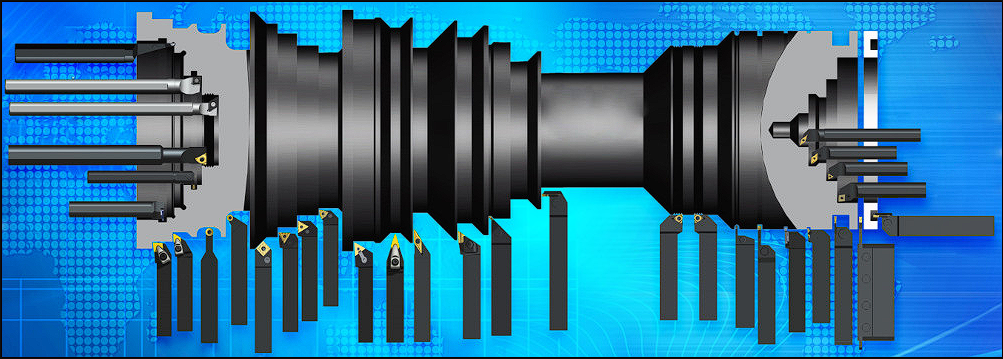
5. После анализа данных перечисленных выше, приступают к выбору режимов резания, состоящего из трех основных элементов (рис. 1.): глубины резания, рабочей подачи и скорости резания.
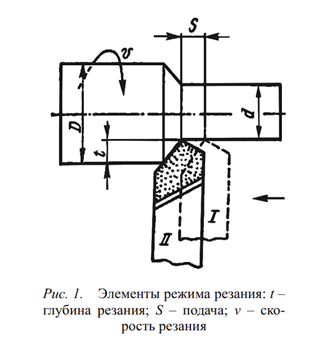
- Глубина резания t, (мм) – толщина срезаемого слоя металла за один рабочий ход резца. При обтачивании ее вычисляют по формуле
t = (D – d) / 2
где D – диаметр обрабатываемой поверхности, мм; d – диаметр обработанной поверхности, мм.
- Подача на оборот Sn, (мм/об) при точении — это путь, пройденный инструментом за один оборот заготовки. Кроме подачи на оборот, при точении рассматривается еще минутная подача Sf (мм/мин) — путь, пройденный инструментом за 1 минуту:
S f = S n × n,
где n — частота вращения шпинделя
Подачу выбирают в зависимости от:
- марки обрабатываемого материала,
- размеров заготовки,
- выбранной глубины резания,
- геометрии режущей кромки
- типа резца
- рекомендаций производителя инструмента
При черновой обработке ее значение ограничивается жесткостью детали, инструмента и станка. Подача для чистовой обработки определяется главным образом шероховатостью обрабатываемой поверхности. Это же правило применимо и к выбору глубины резания.
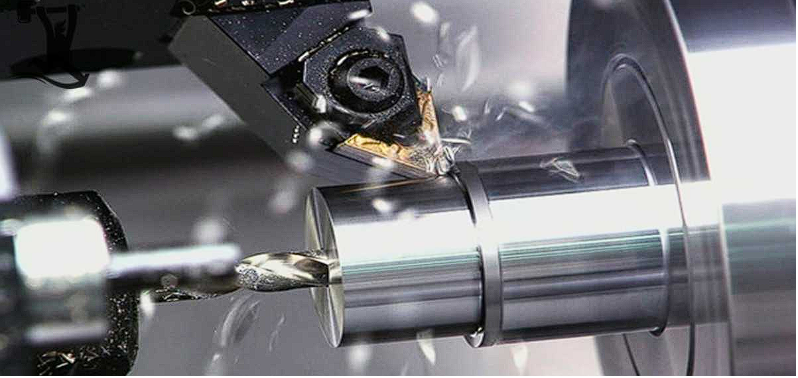
- Скорость резания V,(м/мин) – путь, проходимый наиболее удаленной от центра точкой поверхности резания относительно резца в минуту. Она определяется по формуле
V = πDn / 1000 ≈ Dn / 320,
где V – скорость резания, м/мин; D – наибольший диаметр касания инструмента с заготовкой, мм.
Скорость резания, допускаемая инструментом, определяется заданной стойкостью резца, глубиной резания, подачей, твердостью обрабатываемого материала и рядом других факторов. Средняя стойкость резца обычно принимается равной 15–60 мин.
6. Проверку режима резания по мощности при черновом точении можно выполнить, пользуясь формулой
Nрез = Pz V / 60 * 1020,
где V – скорость резания, м/мин.; 1020 – коэффициент перевода Н x м/с в кВт; Pz – вертикальная составляющая силы резания, Н.
Вертикальная составляющая силы резания Pz (Н) – сила сопротивления резанию, действующая в вертикальном направлении касательно к поверхности резания. Для приближенных расчетов ее можно определить из формулы
Pz = KtS,
где K – коэффициент резания, равный силе резания, приходящейся на 1 мм2 площади поперечного сечения срезаемой стружки, МПа (табл. 1);
t – глубина резания, мм; S – подача, мм/об.
Таблица 1
Среднее значение коэффициента резания К при точении
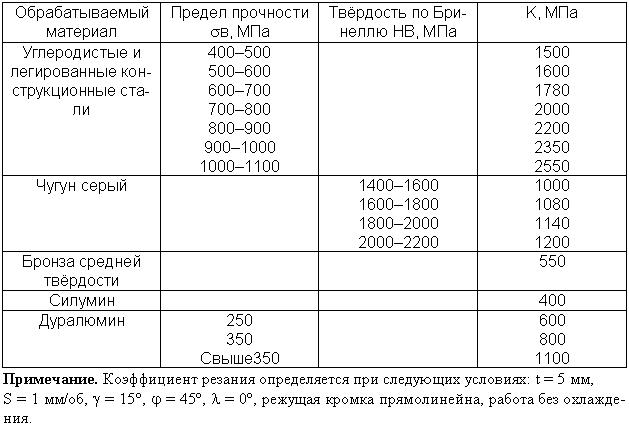
7. После подсчета мощности резания должно быть обеспечено условие по формуле
Nрез≤Nэ.д.η.
Значение КПД η берется из паспорта станка, либо значение эффективной мощности на шпинделе Nэ.дη, соответствующее принятому на предыдущем этапе расчета режима резания значению фактического числа оборотов шпинделя.
На данном этапе производятся корректировки режимов резания (если это требуется) исходя из полученных данных.
8. Определение основного времени. Для оценки эффективности выбранного режима резания производится расчет основного времени.
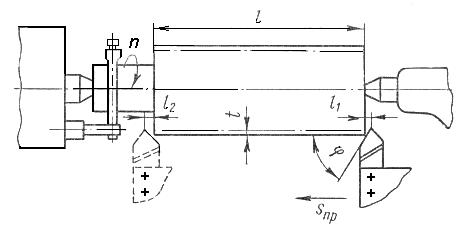
Рис. 2. Схема к расчёту основного технологического времени при обтачивании цилиндрической поверхности
Основным технологическим (машинным) временем называется время, затрачиваемое непосредственно на процесс изменения формы и размеров заготовки и получение поверхности требуемой шероховатости. В общем случае время равно пути делённому на скорость. Путь при точении – это длина обработки, скорость – это скорость подачи в м/мин, равная произведению nS. Следовательно, при токарной обработке основное технологическое время То (мин) определяется по формуле
То = Li / nS,
где L – расчётная длина пути режущего инструмента в направлении подачи, мм; i – число проходов; n – частота вращения заготовки, об/мин; S – подача, мм/об.
L = l + l1 + l2,
где l – расчетная длина обрабатываемой поверхности, мм;
l1 = t * ctgj – величина врезания резца, мм;
t – глубина резания, мм; j - главный угол в плане резца;
l2 = 1–3 мм – выход (перебег) резца.