Фрезерование — это важнейший процесс в механической обработке, который используется для создания высокоточных изделий и деталей на фрезерных станках. Эта операция требует не только теоретических знаний, но и практических навыков в настройке станка, подборе режимов резания, а также в выборе инструмента и способе крепления заготовок.
Основные виды работ на фрезерных станках
Фрезерный станок выполняет множество различных операций, таких как обработка торцевых, плоских, фасонных и других сложных поверхностей. С его помощью можно осуществлять следующие работы:
- Обработка торцевых и плоских поверхностей
Такие работы выполняются с использованием торцевых и цилиндрических фрез. - Нарезка канавок и пазов
Для этих операций используются концевые фрезы, которые позволяют с высокой точностью выбирать материал по заданной глубине. - Обработка сложных форм
Фасонные фрезы применяются для создания нестандартных геометрий, таких как углы, радиусы или другие криволинейные элементы. - Обработка шлицевых соединений
Черновое фрезерование шлицев на валах может осуществляться дисковыми фрезами, а чистовое специальной червячной фрезой, которая обеспечивает наибольшую точность. - Сверление и нарезка резьбы
Свёрла, фрезы и метчики позволяют создавать отверстия под резьбу и другие специфические элементы.
Важно учитывать, что для каждой из операций необходимы свои режимы резания и типы фрез, что влияет на производительность и качество обработки.
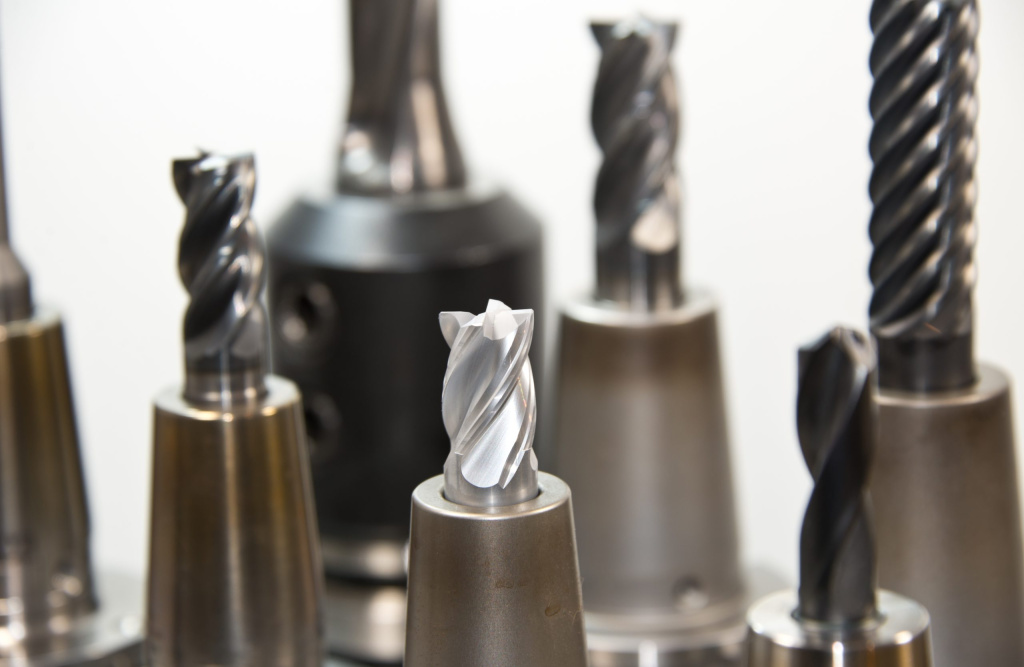
Типы фрез и их назначение
Фрезы бывают разных типов в зависимости от их формы, назначения и метода крепления. В таблице ниже показано, как выбрать подходящий инструмент для различных операций на фрезерном станке.
Типы фрез и их характеристики
Тип фрезы | Назначение | Применение | Особенности |
Цилиндрические | Обработка плоских и торцевых поверхностей | Применяются для фрезерования прямых поверхностей, строго вертикальных граней и канавок. | Могут иметь прямые или винтовые зубья, они универсальны. |
Торцевые | Обработка торцевых и плоских поверхностей | Формировании плоскостей на обрабатываемой заготовке при различных видах обработки. | Работают как торцевой частью и в малой степени периферией. |
Фасонные | Обработка сложных форм и профилей | Изготовлении деталей, с большим соотношением длины и ширины. |
Могут иметь две конструкции зубьев: -затылованную, -остроконечную |
Концевые | Создание пазов, уступов, углов | Для глубокой обработки и чистовой фрезеровки | Позволяют работать с узкими участками, высокой точностью |
Червячные | Нарезания зубьев на цилиндрических зубчатых колесах, особенно с косыми или прямыми зубьями | Производство зубчатых колес: цилиндрических, косозубых, с внешними и внутренними зубьями. | Можно нарезать различные типы зубьев и модулей с минимальными отклонениями по форме и шагу. |
Дисковые | Грубой обработки металла и дерева. | Распиливание материала и вырезание пазов определённой ширины и глубины. | Несколько подвидов: отрезные, прорезные, пазовые, имеют небольшую ширину. |
Эти фрезы очень важны в фрезерной обработке. Каждый тип имеет свои особенности и используется в разных ситуациях. Правильный выбор инструмента зависит от формы, размера и нужной точности детали.
Параметры резания и их влияние на качество обработки
При работе с фрезерными станками необходимо правильно настроить параметры резания. Основные из них:
• Скорость резания (Vc):
Это скорость, с которой точка на режущей кромке фрезы движется по заготовке. Расчет скорости резания производится по формуле:
Vc = π × D × n
где:
- D — диаметр фрезы,
- n — частота вращения инструмента в оборотах в минуту.
Для различных материалов скорость резания варьируется. Например, для стали скорость резания может быть в пределах 50-100 м/мин, а для алюминия — до 500 м/мин.
• Глубина резания:
Это расстояние от верхней точки обрабатываемой заготовки до нижней точки реза. Глубина резания влияет на нагрузку на инструмент и качество поверхности. Обычные значения для глубины резания колеблются от 0,1 до 3 мм на один проход.
• Ширина резания:
Это расстояние между сторонами реза. Чем больше ширина, тем выше нагрузка на инструмент, и тем больше требуется мощность станка.
• Подача на зуб (fz):
Подача на зуб — это величина перемещения детали за один оборот фрезы. Определяется по формуле:
Fz = f / z
где:
- f — подача на оборот,
- z — количество зубьев фрезы.
Подача влияет на качество поверхности и износ инструмента.
• Подача:
Подача — это скорость перемещения заготовки или инструмента по направлению обработки. Подача также влияет на время обработки и качество поверхности.
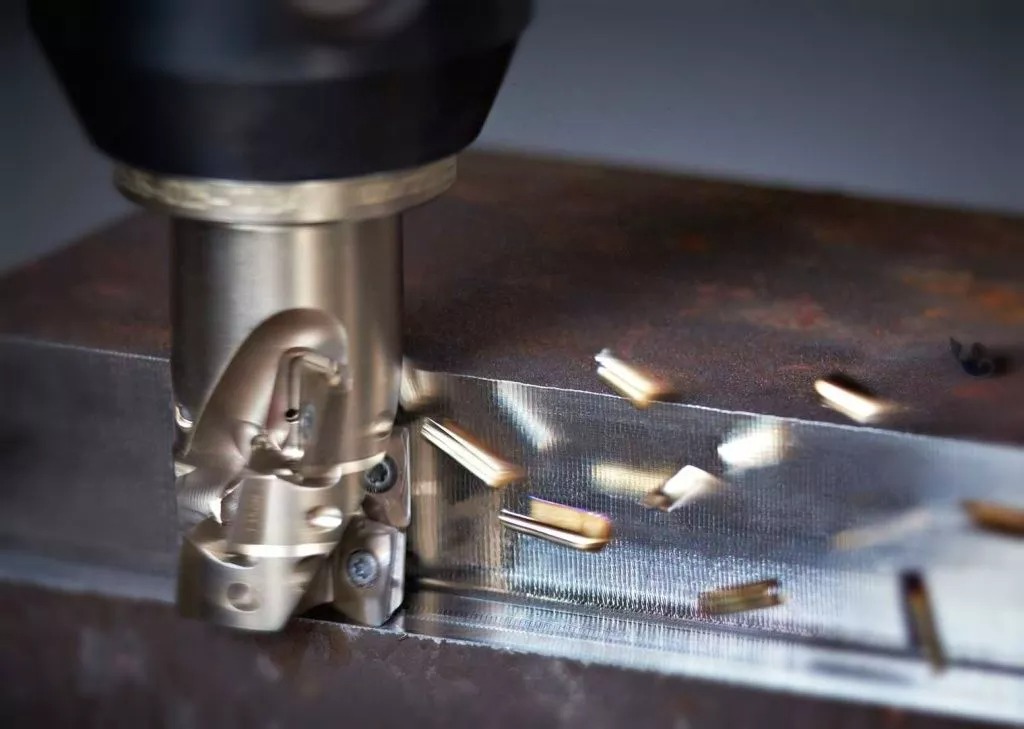
Рекомендуемые параметры для обработки различных материалов
Ниже приведены таблицы с оптимальными параметрами резания для различных материалов, что позволяет обеспечить максимальную производительность и качество обработки на фрезерном станке.
ISO | Обрабатываемы материал |
Твёрдость HB |
Скорость резания Vc(м/мин) Min. – средняя – Max. |
Подача fz(мм/зуб) Min. – средняя – Max. |
Глубина резания, (мм) |
P | Углеродистая сталь | 145-195 | 100-160-200 | 0.2 - 0.3 - 0.4 | 0.5 - 3.0 |
Легированная сталь | 185-210 | 100-140-180 | 0.1 - 0.2 - 0.4 | 0.5 – 2.5 | |
M | Нержавеющая сталь | 180-240 | 80-120-160 | 0.1 - 0.2 - 0.3 | 0.5 – 1.0 |
K | Чугун | 130-260 | 80-120-160 | 0.1 - 0.2 - 0.4 | 0.5 – 2.0 |
N | Цветные металлы | 75-130 | 200-500-800 | 0.1 - 0.3 - 0.4 | 0.5 – 3.0 |
S | Жаропрочные | 200-320 | 80-120-160 | 0.1 - 0.3 - 0.4 | 0.5 – 2.0 |
Примечания | Режимы резания ориентировочные. Назначенные режимы резания должны выбираться согласно рекомендаций производителя конкретного инструмента. |
Влияние негативных факторов на качество обработки
Несмотря на высокую производительность и точность, фрезерование подвержено нескольким факторам, которые могут негативно повлиять на качество обработки:
- Вибрации:
Вибрации возникают при высоких скоростях резания, использовании неправильно подобранного инструмента с большими вылетами. Это приводит к снижению точности обработки и ухудшению шероховатости поверхности. - Износ инструмента:
При длительной работе фрезы её режущая способность ухудшается, что приводит к увеличению трения, перегреву, возрастанию нагрузки на шпиндель и, как следствие, снижению качества обработки. Регулярная замена инструмента или корректировка режимов резания необходимы для поддержания высокой точности. - Перегрев:
Перегрев в зоне резания приводит к образованию наклепов на поверхности заготовки, что может повлиять на её механические свойства. Для предотвращения перегрева используются системы подачи Смазочно-охлаждающей жидкости (СОЖ), воздуха, масла. - Неправильная фиксация заготовки:
Недостаточно надежное закрепление заготовки может привести к её перемещению во время обработки, что также может стать причиной появления брака и увеличения дефектов на поверхности.
Советы по настройке фрезерного станка
- Регулировка скорости резания:
При установке фрезы важно правильно настроить скорость резания материала, основываясь на соответствии материала режущего инструмента и материала заготовки. Неправильный подбор скорости резания может привести к быстрому износу инструмента. - Подача и глубина резания:
Для эффективной обработки всегда начинайте с более мелких значений подачи и глубины резания, постепенно увеличивая их по мере освоения обработки. - Использование охлаждения инструмента:
Охлаждение инструмента крайне важно для предотвращения перегрева и износа фрезы. Они также способствуют отведению стружки от зоны резания. - Проверка и калибровка инструмента:
Перед началом работы убедитесь, что фреза и оправка установлена правильно и отсутствует биение.
Работа на фрезерном станке требует внимательности и профессионального подхода к выбору инструментов, настройке режимов резания и качественному контролю процесса. Понимание того, как различные параметры влияют на обработку, позволит значительно повысить производительность и качество работы фрезерного станка.